- 上海那艾實驗儀器有限公司
- 網址:xc55.net
形狀的通孔,還可以拉削平面及各種組合成形表面。圖8.3.13為適用于拉削加工的典型工件截面形狀。由于受拉刀制造工藝以及拉床動力的限制,過小或過大尺寸的孔均不適宜拉削加工(拉削孔徑一般為10~1000mm,孔的深徑比一般不超過5),盲孔、臺階孔和薄壁孔也不噴霧干燥機適宜拉削加工。 ·330· 圖8.3.13 拉削加工的典型工件截面形狀 1.拉刀根據工件加工面及截面形狀不同,拉刀有多種形式。常用的圓孔拉刀結構見圖8.3.14,其組成部分包括: 圖8.3.14 圓孔拉刀的結構
(1)前柄用以拉床夾頭夾持拉刀,帶動拉刀進行拉削。(2)頸部是前柄與過渡錐的連接部分,可在此處打標記。(3)過渡錐起對準中心的作用,使拉刀順利進入工件預制孔中。(4)前導部起導向和定心作用,防止拉孔歪斜,并可檢查拉削前的孔徑尺寸是否過小,以免拉刀第一個切削齒載荷太重而損壞。 (5)切削部承擔全部余量的切除工作,由粗切齒、過渡齒和精切齒組成。(6)校準部用以校正孔徑,修光孔壁,并作為精切齒的后備齒。 ·331· (7)后導部用以保持拉刀最后正確位置,防止拉刀在即將離開工件時,工件下垂而損壞已加工表面或刀齒。 (8)后柄用作直徑大于60mm既長又重拉刀的后支承,防止拉刀下垂。直徑較小的拉刀可不設后柄。2.拉孔的工藝特點分析前述圓孔拉刀的結構可知,拉刀是一種高精度的多齒刀具,由于拉刀從頭部向尾部方向其刀齒高度逐齒遞增,拉削過程中,通過拉刀與工件之
間的相對運動,分別逐層從工件孔壁上切除金屬(見圖8.3.15),從而形成與拉刀的最后刀齒同形狀的孔。 圖8.3.15 拉刀拉孔過程 拉孔與其他孔加工方法比較,具有以下特點: (1)生產率高拉削時,拉刀同時工作的刀齒數多、切削刃總長度長,在一次工作行程中就能完成粗、半精及精加工,機動時間短,因此生產率很高。 (2)可以獲得較高的加工質量拉刀為定尺寸刀具,有校準齒對孔壁進行校準、修光;拉孔切削速度低(v=2~8m/min),拉e 削過程平穩(wěn),因此可獲得較高的加工質量。一般拉孔精度可達IT8~IT7級,表面粗糙度Ra值為 1.6~0.1μm。(3)拉刀使用壽命長由于拉削速度低,切削厚度小,每次拉削過程中,每個刀齒工作時間短,拉刀磨損慢,因此拉刀耐用度高,使用壽命長。 (4)拉削運動簡單拉削的主運動是拉刀的軸向移動,而進給運動是由拉刀各刀齒的齒升量f(見圖8.3.15)來z 完成的。因此,拉床只有主運動,沒有進給運動,拉床結構簡單,操作方便。但拉刀結構較復雜, ·332· 制造成本高。拉削多用于大批量或成批生產中。 3.拉床拉床按用途可分為內拉床及外拉床,按機床布局可分為臥式和立式。其中,以臥式內拉床應用最為普遍。圖8.3.16為臥式內拉床的外形結構。液壓缸1固定于床身內,工作時,液壓泵供給壓力油驅動活塞,活塞帶動拉刀4,連同拉刀尾部活動
支承5一起沿水平方向左移,裝在固定支承上的工件3即被拉制出符合精度要求的內孔。其拉力通過壓力表2顯示。 拉削圓孔時,工件一般不需夾緊,只以工件端面支承,因此,工件孔的軸線與端面之間應有一定的垂直度要求。當孔的軸線與端面不垂直時,則需將工件的端面緊貼在一個球面墊板上,如圖 8.3.17所示,在拉削力作用下,工件3連同球面墊板2在固定支承板1上作微量轉動,以使工件軸線自動調到與拉刀軸線一致的方向。圖8.3.16 臥式內拉床 1—液壓缸;2—壓力表;3—工件;4—拉刀;5—活動支承 圖8.3.17 拉圓孔的方法 1—固定支承架;2—球面墊板;3—工件;4—拉刀 8.3.5 內圓表面磨削加工內圓表面的磨削可以在內圓磨床上進行,也可以在萬能外圓磨床上進行。內圓磨床的主要 ·333· 類型有普通內圓磨床、無心內圓磨床和行星內圓磨床。不同類型的內圓磨床其磨削方法是不相同的。 1.內圓磨削方法(1)普通內圓磨床的磨削方法普通內圓磨床是生產中應用最廣的一種,圖8.3.18所示為普通內圓磨床的磨削方法。磨削時,根據工件的形狀和尺寸不同,可采用縱磨法(見圖a
)、橫磨法(見圖b),有些普通內圓磨床上備有專門的端磨裝置,可在一次裝夾中磨削內孔和端面(見圖c),這樣不僅容易保證內孔和端面的垂直度,而且生產效率較高。 圖8.3.18 普通內圓磨床的磨削方法 如圖a所示,縱磨法機床的運動有:砂輪的高速旋轉運動作主運動n;頭架帶動工件旋轉作 s 圓周進給運動f,砂輪或工件沿其軸線往復作縱向進給運動f,在每次(或幾次)往復行程后,工
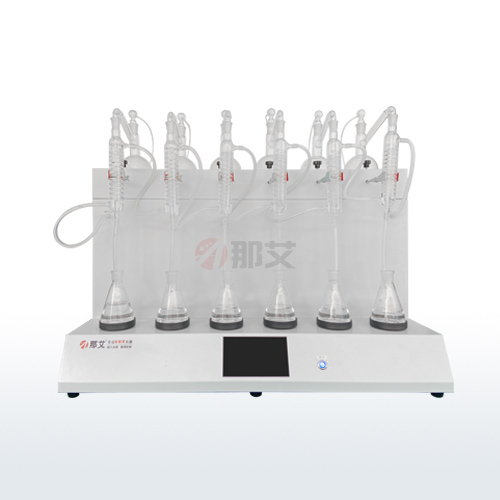
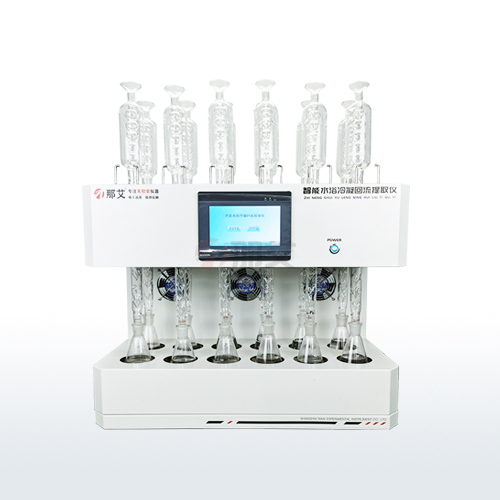
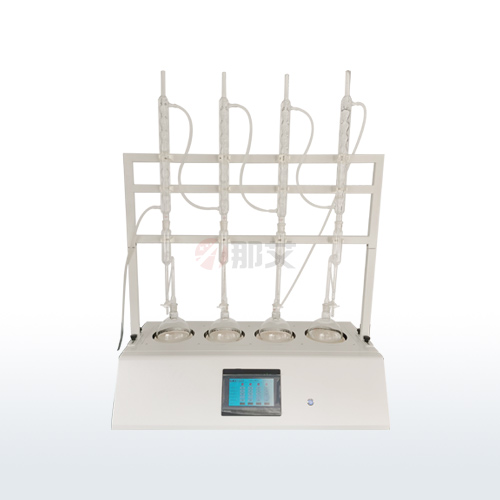
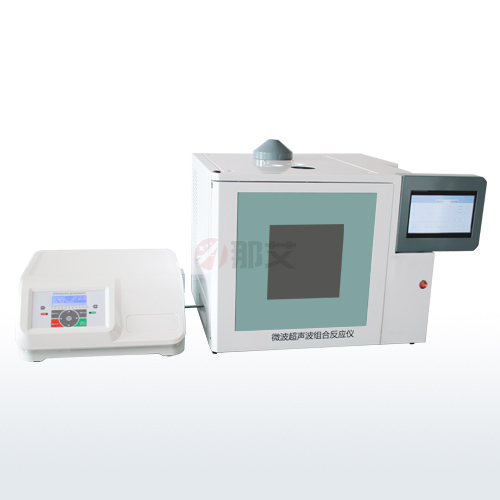